Motores eléctricos de alto desempeño: hacer más con menos energía
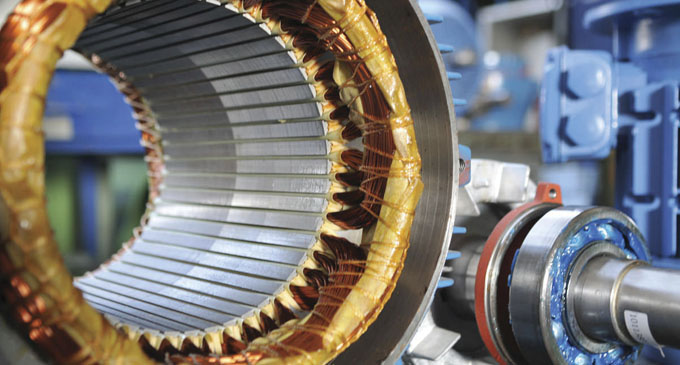
En el sector industrial, los motores eléctricos son el componente con el mayor consumo de energía. Esto resulta un problema si su eficiencia es baja, pues requerirán más electricidad para realizar su trabajo y mucha se desperdiciará en forma de calor. Al mismo tiempo son un nicho de oportunidad, toda vez que reemplazarlos por equipos de alto desempeño disminuye el consumo y los costos de facturación eléctrica
Por Christopher García
A escala mundial, el sector industrial es el que menor número de usuarios registra con las compañías suministradoras y el que consume más energía. En países desarrollados, como Alemania, Japón o Estados Unidos, la industria es responsable por el consumo de 60 por ciento de la energía total que genera cada país, según afirma el maestro Enrique Balan, consultor de ICA Procobre, especialista en calidad de energía y sistemas de tierra física y perito en energías renovables. En el caso de los países menos desarrollados, como México, la situación es prácticamente la misma, al consumir la industria entre 40 y 45 por ciento del total de energía generada, según asegura el experto.
Por otro lado, entre los sistemas que se utilizan en este sector, los motores eléctricos son los equipos que mayor energía consumen. Se trata de un rasgo que no puede modificarse, debido a que son los encargados del trabajo mecánico; no obstante, el maestro Balan asegura que sí es posible reducir su consumo de energía al reemplazarlos por equipos con mejor tecnología y mayor eficiencia.
El consultor de ICA Procobre explica que muchas fábricas –incluso muchos hogares– cuentan con motores eléctricos con una antigüedad de hasta 30 años, que siguen en funcionamiento porque aún cumplen su función, pero su consumo de energía es poco eficiente. “La norma que cubre los motores eléctricos, que es la NOM-0016-SENER-2010, se modificó en los porcentajes de eficiencia, con lo que aumentó aproximadamente 6 por ciento el nivel exigido respecto de la norma de 1997”, señala Balan. Este cambio implica que aquellos motores fabricados hasta antes de 2010 es muy probable que no ofrezcan la eficiencia energética que brindan los más avanzados.
Mucho de esto tiene que ver con el desarrollo tecnológico. En los últimos años se han fabricado motores con desempeños más altos y consumos de energía menores, sin afectar el trabajo que desempeñan. “Aquellos industriales que tienen motores de tipo estándar están consumiendo 6 o 7 por ciento más de energía que si tuvieran uno de alta eficiencia o eficiencia premium. Son motores que tienen diferencias en la composición de sus elementos y la calidad de fabricación es mucho mejor”, comenta el especialista.
Dicho de otro modo, los usuarios industriales se encuentran ante un panorama de optimización del consumo de energía con el reemplazo de un componente. De hacerlo, además de impactar positivamente sus balances financieros por la reducción de la facturación eléctrica, el beneficio se extiende, por ejemplo, hacia el ambiente, pues al requerir menos energía se necesita generar menos electricidad, que hasta ahora sigue dependiendo en casi 80 por ciento de los combustibles fósiles, principales responsables de las emisiones de bióxido de carbono a la atmósfera.
Por supuesto, reemplazar un motor antiguo por uno mejorado o elegir un motor de alto desempeño por encima de uno de calidad estándar exige una inversión mayor. Esta diferencia de costo puede derivar en que el usuario decida no utilizar un motor de alta eficiencia. Lo cierto es que, a largo plazo, adquirir un motor de alta eficiencia ofrece beneficios tanto económicos como operativos.
“A veces vemos equipos de alta eficiencia cuyo precio es hasta 20 por ciento mayor; eso impacta al industrial verdaderamente fuerte y deberá decidir si lo paga de inicio o cada año, en la factura de la energía eléctrica que le llegará más alta. Pero hay que tomar en cuenta también que un buen estudio de costos muestra que la inversión adicional se recupera en dos o tres años, y durante los siguientes años de vida del motor obtenemos, llamémosle así, un ahorro; no es un ahorro realmente, sino que no se desperdicia la energía”, explica Balan.
En este sentido, la eficiencia energética de un motor debe entenderse como la capacidad de “hacer más, con el menor esfuerzo posible. Se trata de convertir la misma energía en kilowatts que consume en energía mecánica. Un motor eficiente es el que transforma toda la energía eléctrica que recibe en energía mecánica útil. Si un motor tiene una eficiencia de 90 por ciento, gasta 100 por ciento de energía eléctrica, pero sólo convierte 90 por ciento en energía mecánica. Ahí, el motor está perdiendo 10 por ciento y es como si tuviéramos un agujero en la cartera: cada vez que recibimos un peso, se caen 10 centavos y no los recuperamos; incluso, perdemos, porque si esos equipos están dentro de oficinas, se genera calor y hay que eliminarlo por medio del aire acondicionado”, describe el especialista.
Cómo aprovechar al máximo los motores de alta eficiencia
La posibilidad de evitar el desperdicio de energía se debe a diversos elementos compositivos, que van desde el diseño y los materiales de fabricación, hasta la implementación de avances tecnológicos que potencian la operación del motor. “Por ejemplo –comenta Balan–, el acero con el que se fabrica el cierre del motor es acero al silicio, que tiene mejores propiedades magnéticas que el acero en motores tipo estándar. Otro rasgo es la mayor cantidad de cobre en sus bobinas, el cual es de mayor sección transversal; con eso, se logran reducir las pérdidas en el cobre. El laminado es más delgado, con lo que disminuyen las pérdidas del núcleo. También el núcleo es de mayor longitud, la distancia entre el rotor y el estator es mucho menor, casi están rozando, eso obliga a pensar que la fabricación tiene un cuidado mucho mayor. Las aletas de enfriamiento son de mejor calidad y sus rodamientos son antifricción. En otras palabras, los motores de alta eficiencia tienen características de mejora tecnológica, incluso la fabricación es hecha por medio de robots, lo que implica mayor precisión”.
El primer paso, entonces, es la correcta selección del motor. De acuerdo con el maestro Balan, se debe elegir de tal modo que opere entre 75 y 90 por ciento de su potencia nominal. “Un ejemplo muy claro de esto son los elevadores: a veces, cuando en un elevador va una persona, el motor trabaja al 30 o 35 por ciento, y esto disminuye su eficiencia”.
Por otro lado, al instalar un motor se debe estar seguro de que la caída de tensión en los conductores de alimentación no es muy elevada. “Hay que recordar que la norma de instalaciones eléctricas recomienda que la caída de tensión sea del 5 por ciento. Pero, claro, la persona que realiza el proyecto puede ajustar a 5 o más. Nosotros recomendamos que ese valor nunca se utilice, sino que se estime en 1 o 2 por ciento, con eso se logra que el motor trabaje en una situación óptima”, apunta el consultor de ICA Procobre.
Respecto de la tensión, balancearla representa un punto importante, ya que, explica Balan, “para los industriales, una diferencia de tensión para un motor trifásico de 2 por ciento incrementa las vibraciones, las pérdidas en motor, la caída de tensión en el mismo motor y, por supuesto, reduce su vida útil”.
Las vibraciones son también un aspecto que se debe vigilar con atención, a fin de evitarlas siempre que sea posible. “Muchas veces, la flecha, que de alguna forma se acopla a la carga, podría tener una pequeña desviación en su trayectoria, esto provocaría vibraciones. Entonces, el mantenimiento es sumamente importante, porque las bandas van moviendo ligeramente la posición del motor cuando no están bien sujetos. Un indicador que se debe buscar es que los motores tengan sello Fide o NEMA Premium”, recomienda el especialista.
En general, los elementos compositivos del equipo son invisibles para el usuario. En este sentido, buscar el sello Fide es una herramienta útil para seleccionar el mejor motor, toda vez que garantiza la existencia de un proceso de revisión realizado por un tercero y permite evaluar con cierto grado de certeza que la eficiencia ofrecida por el motor es fidedigna. “Quizás en una misma planta se fabrican motores de diversas capacidades, de 1 HP o de 100 HP, y es posible que tengan motores de líneas económicas y motores de líneas finas. Entonces, sería bueno que el proyectista verificara no sólo la potencia, la tensión de operación o el número de fases con las que va a trabajar, sino la eficiencia energética”, sugiere el maestro Balan.
Cuándo reemplazar un motor
La antigüedad de un motor es un buen punto de partida para evaluar si debe reemplazarse por uno nuevo. Sin embargo, si bien el desgaste de los componentes como resultado del trabajo es inevitable, el motor seguirá ofreciendo el servicio necesario. Enrique Balan señala que es muy difícil que los motores modifiquen su eficiencia o dejen de funcionar si la carga que soportan no ha sido modificada. El tema es que si el motor tiene una eficiencia baja, seguirá trabajando con baja eficiencia.
“Normalmente, el motor no empieza a fallar y a disminuir su capacidad. Una persona, a los 20 años, corre muy rápido y a los 60, menos, pero eso no lo podemos observar en un motor. Lo que sucede en un motor es que se acaban los rodamientos y hay que cambiarlos. El técnico de mantenimiento deberá de hacer pruebas, por ejemplo, de vibración para observar que no ha incrementado sus movimientos; luego, de aislamiento, observando que, en el interior, el polvo, la humedad o cualquier tipo de basura no estén colocadas entre las partes eléctricas y haya fugas de energía”, explica el especialista y señala que por lo regular los fabricantes ofrecen tablas de durabilidad, en las que se indica cuándo será necesario cambiar los rodamientos.
Caso distinto es cuando un motor falla o deja de funcionar. Anteriormente, si esto sucedía, la solución era llevar el motor a reparar en cualquier taller que pudiera realizar el trabajo. Con los motores de alta eficiencia esto resulta un problema y se corre el riesgo de que su eficiencia disminuya. Esto se debe a dos puntos importantes: “El primero de ellos es que cuando el conductor de cobre se arrolla en su rotor, si es hecho a mano no queda suficientemente estirado; al quedar chuecos los devanados, se generan pérdidas adicionales por calentamiento en el conductor. Por otro lado, cuando no alcanza el cobre porque se hizo bola, lo cortan antes y el motor tiene menos cantidad de cobre, esto hace que consuma más corriente eléctrica”.
En el caso del laminado de acero, explica el especialista, muchas veces es necesario separarlo para hacer reparaciones; “al momento de volverlo a juntar, si no está completamente limpio, quedan algunas separaciones entre laminados y a la hora de barnizarlo y hornearlo esos grumos aumentarían las pérdidas de laminado”.
La diferencia entre inversión y gasto
La industria encuentra una oportunidad de reducir su consumo eléctrico en el reemplazo de motores. En los proyectos de renovación o construcción de nuevas plantas, los industriales dueños de empresas no son quienes adquieren los productos. Esta labor suele quedar en manos de los proyectistas o contratistas, quienes tomarán la decisión de ofrecer un mejor motor al cliente, con un costo mayor.
“A veces, para poder ganar un proyecto, se reducen los costos, aumentando las pérdidas. En los grandes complejos industriales, que no ven directamente el equipo, sino que contratan despachos de ingeniería, son los despachos los que toman la decisión de ofertarle a su cliente equipos de mayor capacidad y de mejores características en el consumo eléctrico”, describe Balan.
En este contexto, el costo de inversión es siempre un tema por considerar. Si un proyecto aumenta su costo inicial, es difícil que el inversionista evalúe con detenimiento que una inversión mayor le redundará en beneficios a largo plazo. Esto representa un obstáculo para la eficiencia en varios sentidos. México sigue siendo un mercado de precios; sólo hasta fechas recientes se han comenzado a evaluar los proyectos en su ciclo de vida total, si bien es una sección mínima de los inversionistas quienes lo están implementando. “Si recordamos que los industriales son los que mayor cantidad de energía consumen, ellos serían los candidatos idóneos para entender esta situación. Ellos tendrían que exigir a sus asesores energéticos la entrega de dos proyectos: uno con características estándar y uno con características óptimas”.
Por otro lado, “cuando el proyectista hace su proyecto, debería alimentar ese motor eléctrico con cableado de tal suerte que no tenga 5 por ciento de caída de tensión, como lo recomienda la norma, sino que tenga 1 o 2 y que se lo explique al cliente para que él pueda tomar una decisión informada”.
En este tema, Balan reconoce que las generaciones más jóvenes son las más conscientes de esta diferencia y, sobre todo a nivel doméstico, miran más allá del costo inicial. “Hemos observado que las casas de personas jóvenes, de 30 años para abajo, tienen equipamiento de alta eficiencia y no se van por el precio. Las personas de mayor edad, en cambio, siguen pensando en que el precio es un punto importante. Esto tiene que ver con que las generaciones jóvenes asimilan los cambios con mayor velocidad. Ellos están conscientes de que existe un problema mundial con el cambio climático y actúan, no esperan”.
A manera de resumen, el maestro Balan recomienda tomar en cuenta las características del motor al adquirirlo y cuidar que todos los elementos de la instalación cuenten con características que no actúen en detrimento de su eficiencia. “Brindarle al motor el mantenimiento periódico que indica el fabricante, cambiándole los rodamientos y verificando que la carga no haya excedido la capacidad del motor, es algo que no se debe olvidar”.