Sincronía sobre ruedas
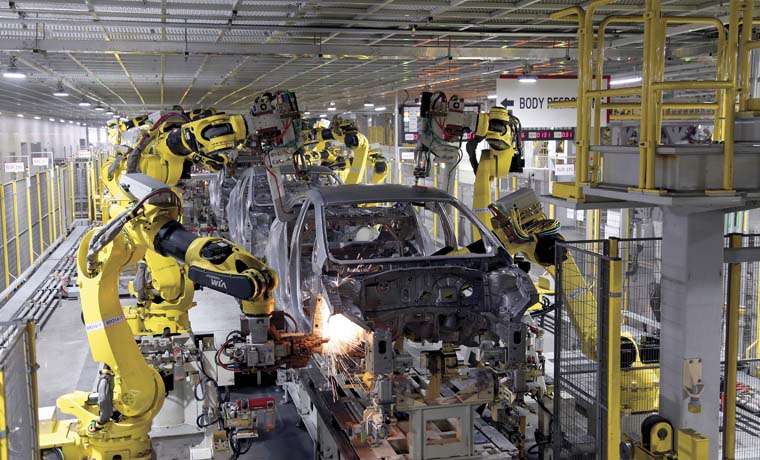
Suave, rauda y flexible, así es la conducción de la planta KIA Motors México, en el municipio de Pesquería, en Nuevo León. Con una línea de ensamblaje y producción completamente digitalizada con la Digital Enterprise Suite de Siemens y sincronizada con la gestión de energía de la planta, bajo el concepto Total Integrated Power, su manejo y operación satisface las más altas exigencias en términos de fiabilidad y eficiencia energética
Por Irayda Rodríguez / Fotografías cortesía de Siemens
Corear del Sur, 1944, nace Kia Motors, un gigante automotriz que, en sus inicios, ensamblaba motocicletas para una empresa japonesa en una fábrica de tuberías de acero. Siete décadas más tarde, las cosas son muy diferentes, pues se ha convertido en uno de los principales jugadores de la industria y está considerada una de las 100 mejores compañías del mundo, con una producción cercana a los 3 millones de vehículos anuales y presencia en países como China, Estados Unidos y algunas naciones europeas.
Acorde con su compromiso de producir automóviles de alta calidad y diseño innovador, en julio de 2015 siguió adelante con su expansión global al incursionar en el mercado mexicano. Un año más tarde, inauguró una enorme planta de producción a 10 kilómetros del municipio de Pesquería, en Nuevo León.
Esta fábrica automotriz está programada para producir 300 mil vehículos durante su primer año de servicio, y es considerada la más moderna de las instalaciones de producción de KIA en el mundo.
El proyecto dispuso de una serie de requerimientos precisos para una solución de suministro de energía que fuera fiable, flexible y eficiente. Su edificación, prácticamente contra reloj, representó el proyecto greenfield construido con mayor rapidez en la historia del gigante automotriz.
Una solución poderosa y totalmente integrada
Víctor Alemán, gerente de Relaciones Públicas de KIA Motors México, cuenta que el proceso de construcción duró poco más de un año, para que el arranque de operaciones se hiciera efectivo a partir de mayo de 2016.
Seis meses antes de su apertura, la empresa alemana Siemens comenzó los trabajos para proporcionar un sistema de distribución eléctrica que cumpliera cabalmente con los requerimientos del proyecto. El tamaño de la planta y la necesidad del cliente de que tuviera máxima flexibilidad hicieron del proyecto todo un desafío. Pero Siemens se las arregló, y proporcionó un sistema de protección y medición en un corto plazo de entrega.
“Desde el principio fue necesaria una planificación precisa y elaborada para diseñar un sistema de distribución de energía, que pudiera adaptarse fácilmente a los cambios en el proceso de producción. Al mismo tiempo, el suministro de energía tenía que satisfacer las más altas exigencias de fiabilidad y eficiencia energética para garantizar el funcionamiento seguro y económico de la planta”, detalló la compañía alemana en un boletín de prensa.
De la mano de KIA Motors, Siemens desarrolló entonces una solución integral respaldada por el concepto de Total Integrated Power (TIP). Esta plataforma proporcionó una sofisticada planeación, dimensionamiento y servicio, así como productos de alta calidad a partir de una sola fuente, desde la planeación, entrega e instalación, hasta su puesta en marcha.
El principal beneficio de este concepto es que integra tecnología de vanguardia en automatización, además de un soporte enfocado en la planeación del sistema, lo que a su vez permitió asegurar la ejecución eficiente del proyecto a partir de los más altos estándares de construcción. El alcance de entrega de esta nueva planta incluyó todos los equipos de subestación de energía para el sistema de distribución eléctrica en media y baja tensión.
Digitalización que dispara la productividad
Iván Pelayo, vicepresidente ejecutivo de las divisiones Process Industries & Drives de Siemens México, Centroamérica y El Caribe, asegura que la inclusión de procesos digitales en una planta productiva forma parte de la denominada Industria 4.0. Dicho concepto alude a una Cuarta Revolución Industrial, que hará más eficientes los procesos de producción de las empresas. En el caso de KIA Motors México, su objetivo es mejorar la calidad y conducir a un alza inmediata en la productividad, con una cifra estimada de 25 por ciento anual.
“En Siemens tenemos un portafolio muy completo de soluciones dedicadas a lo digital. Por ejemplo, hoy podemos diseñar cualquier producto de forma virtual, para luego generar un ambiente de prueba y probarlo; si se presenta alguna falla, también podemos corregirlo de forma virtual. Si logramos digitalizar la industria automotriz, México podría convertirse en la quinta economía más fuerte del mundo, en los próximos 5 años”, afirma Pelayo.
Este centro de manufactura, agrega, es una muestra clara de a dónde se dirige el sector en temas digitales, y evidencia que la tecnología no está peleada con los procesos manuales y abre un abanico de posibilidades en las líneas de producción.
“El sector automotriz –indica Pelayo– posee una ventaja: mediante la digitalización se puede reducir hasta un 50 por ciento el tiempo que un producto tarda en llegar al mercado. Además, en temas de eficiencia, brinda una flexibilidad incomparable”. El ejecutivo señala que, en el pasado, al momento de fabricar modelos diferentes de una misma línea, era necesario realizar un alto en la producción para cambiar los herramentales.
“Esta parada generaba costos. En la actualidad, es posible que diversos productos o modelos se fabriquen en una sola línea de producción; esto es aplicable en cualquier tipo de industria hoy en día”, comenta Pelayo.
Producción en perfecta sincronía
La planta de Pesquería da luz a los automóviles KIA Forte y Río, ambos en versiones Sedán y Hatchback, aunque con diferentes versiones de equipamiento. Como explica Víctor Alemán, gracias a la solución de Siemens es posible tener paquetes de componentes en la misma línea de producción, una logística complicada cuya base es una herramienta tecnológica como esta.
“Trabajamos con un modelo Just in secuence, es decir no estamos manejando inventarios; conforme se consume el componente en la línea de producción también se alimenta en tiempo real. Para alcanzar ese grado de comunicación con el almacén confiamos plenamente en las herramientas tecnológicas que ayudan a disminuir los márgenes de error”, subraya Alemán.
En total, el 80 por ciento de la planta ha instalado soluciones Siemens para la producción de motores, transmisiones, ensamblaje de vehículos y distribución de energía. Gracias a la estandarización de sus instalaciones, el fabricante surcoreano a reducido los inventarios de partes de repuesto y las inversiones óptimas en capacitación.
“Para nosotros es un orgullo contribuir con lo que hace KIA en México y facilitar los procesos a través de la automatización. Al lograr que máquinas y robots funcionen en sincronía evitamos los errores y, si éstos se presentan, son detectados y corregidos rápidamente”, añade por su parte Pelayo.
Para alcanzar esta sincronía, el software desarrollado por Siemens, Simatic Manager controla los movimientos de los robots presentes en las cuatro áreas de producción: estampado, soldadura, pintura y ensamble.
En la primera de ellas, las grandes hojas de acero rolado en frío son transformadas en piezas clave de la carrocería del automóvil. Durante esta trasformación, se emplea una prensa de 5 mil toneladas de presión, de la que derivan puertas, techo, paneles, cajuela y cofre, entre otras partes.
Para ensamblar las piezas, cerca de 380 robots operan en armonía para unir los puntos de soldadura y dar forma al body o cuerpo del vehículo. Posteriormente, el auto es llevado a la estación de pintura, donde otro ejército de robots se encarga de los acabados del auto, así como de bañarlo con capas protectoras de pintura.
El último paso es el ensamble, un ambiente donde la mano de obra humana convive con la maquinaria para instalar más de 30 mil componentes, entre los que figuran tableros, arneses, rines, motores, trasmisiones y llantas.
“En cada etapa del proceso existen diversos filtros, que nos llevan a cumplir con los más altos estándares de calidad mediante rigurosas inspecciones. El último paso son las pruebas dinámicas en una pista de casi 4 kilómetros de longitud, donde los ingenieros confirman que cada vehículo, de los 68 que se producen por hora, funciona adecuadamente”, cuenta Víctor Alemán.
Más eficiencia: el factor clave
La infraestructura eléctrica de Pesquería, desde el diseño hasta la implementación en media y baja tensión, también fue obra de Siemens. Por ello, cada grupo de planta tiene un Utility Center o Centro de Utilitario, así como cinco subestaciones destinadas para cada área de producción; dos de ellas, específicamente, para el departamento de pintura, el cual cuenta con un generador de respaldo exclusivo para que sus procesos no se detengan.
Durante un recorrido por sus instalaciones, José Magallanes Lira, supervisor de Subestaciones Eléctricas de KIA, explica que esta subestación es el punto neurálgico de la planta, pues desde aquí se maneja el área de compresores, proveedores, chillers, sistemas de enfriamiento, de bombeo, cisternas de agua industrial, potable y contraincendios.
“A esta subestación –expone Magallanes– llega un suministro de 115 kV de la Comisión Federal de Electricidad, que inyecta un voltaje primario de 13.8 kV para las operaciones de la planta. Con las celdas principales de media tensión, alimentamos a las áreas de estampado, soldadura, pintura y ensamble, además del área de proveedores”.
En cuanto a la baja tensión, un transformador se encarga del sistema de bombeo de aire acondicionado, tableros de servicio y alumbrados en estas zonas de la fábrica.
En este Centro Utilitario están instalados 22 tableros de control, mientras que otros 90 están distribuidos a lo largo y ancho del centro de manufactura Pesquería, así como dos generadores de emergencia.
En caso de una interrupción eléctrica, Magallanes señala que un generador de apoyo entra en funcionamiento de forma automática para alimentar los sistemas de alumbrado, zonas de producción, oficinas centrales y cortinas metálicas de las naves industriales. Desde este Centro, además, es posible realizar el monitoreo de cada panel en la planta, voltaje, amperaje, armónicos y energía activa o reactiva.
Alejandro Preinfalk, vicepresidente ejecutivo de las divisiones Energy Management & Mobility de Siemens México, Centroamérica y El Caribe, afirma por su parte que gracias al Total Integrated Power se puede hacer un uso más eficiente de la energía mediante un plan de trabajo que evite picos de consumo.
“La meta es lograr que no toda la maquinaria funcione al mismo tiempo. Para ello, se toman datos del consumo para identificar la cantidad de energía que se consume para cada una de las operaciones; esta información es utilizada de manera inteligente para lograr que el ahorro se vea reflejado. Lo anterior permite un mantenimiento más eficaz, ya que al verificar el estado de los equipos se puede actuar y dar servicio justo cuando la máquina lo necesita”, concluye Preinfalk.
En detalle, la solución de Siemens Total Integrated Power constó de:
- 91 conmutadores en media tensión tipo NXAIR con 10 líneas de conmutación
- 186 de baja tensión tipo FC
- 50 disyuntores de aire 3WL (ACB)
- 38 transformadores de resina de fundición en media tensión
- 30 cuadros de conmutación conformes
- 88 dispositivos de protección 7SJ66
- 88 SIMEAS P855 en conmutadores de 4.16 kV y 13.8 kV
- Centros de carga UL Sentron MCCB y centros de carga disyuntor QP
- Interruptores de seguridad